The production of gummy candy making machine begins with the making of the gummy mix. This mixture usually consists of ingredients such as corn syrup, sugar, gelatin, water, and flavorings. The ingredients are carefully measured and mixed together in a large kettle. The kettle is heated to a specific temperature so that the ingredients combine and form a thick, viscous liquid.
A gummy making machine is an essential tool in the gummy making process. These machines are responsible for mixing, shaping and packaging the gummies we all love to eat. In this article, we will look at the different types of machines used to make fudge and the role they play in the candy making process.
1. Stirring and cooking equipment
The first step in making fudge is mixing and cooking the ingredients. This is where the flavor, color, and texture of the fudge is determined. To achieve the perfect consistency and flavor, specialized mixing and cooking equipment is required. These include stainless steel mixing tanks, cookware and blenders capable of heating, cooling and mixing ingredients to precise specifications.
Mixing and cooking equipment is responsible for mixing ingredients, cooking the mixture to the right temperature, and ensuring that all flavors are evenly distributed. This step is crucial to getting the flavor and texture you want for your fudge.
Once you have your fudge mixture ready, you need to shape it into the familiar fudge shape. This is where deposit machines come into play. Depositing machines are used to pour fudge mixture into molds to form candies of the desired shape and size. These machines are equipped with precision pumps and nozzles that accurately inject the fudge mixture into the molds, ensuring uniform shape and size.
The depositing machine can be customized to produce various shapes of gummy candies, including gummy bears, gummy worms, fruit gummy candies, etc. They are also capable of producing multiple colors and flavors in the same batch, making them versatile and efficient in gummy production.
3. Cooling Tunnel
Once the fondant mixture is placed in the mold, it needs to cool and solidify. Cooling tunnels are used for this purpose, providing a controlled environment for the fudge to solidify. The cooling process is essential to ensure that the fudge retains its shape and texture and is ready for packaging.
The cooling tunnel is designed to promote rapid and even cooling of the gummies and prevent them from sticking or deforming. They also provide a hygienic environment for the candy to set, minimizing the risk of contamination. Cooling tunnels are an important part of the fudge-making process, ensuring that the candies are ready for further processing.
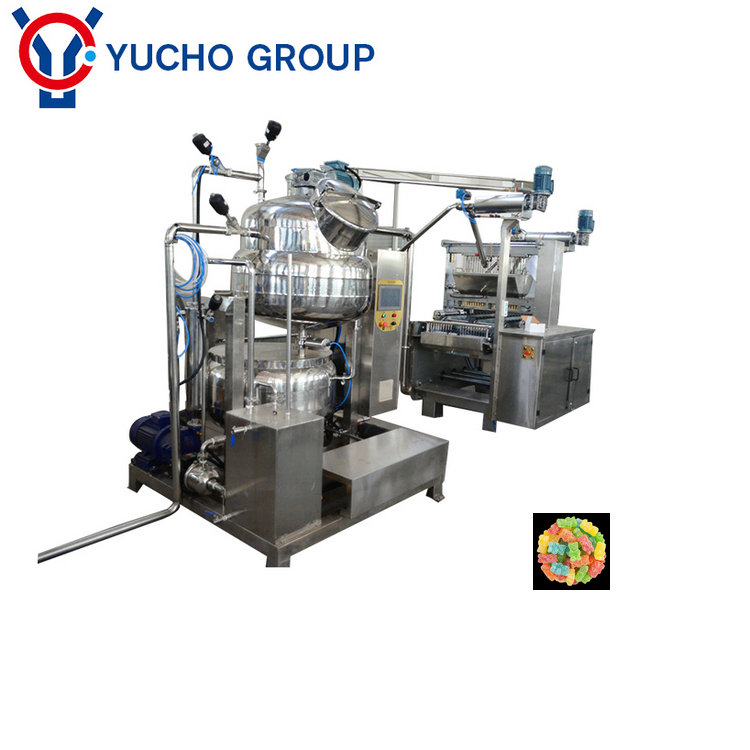
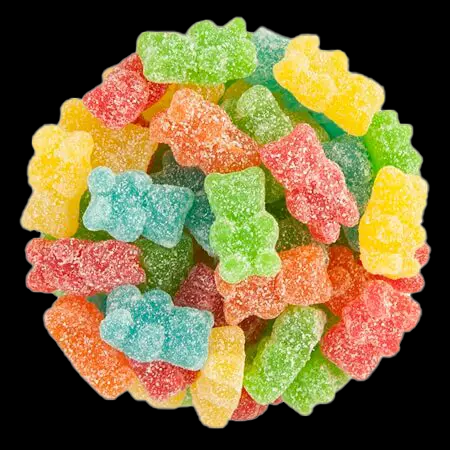
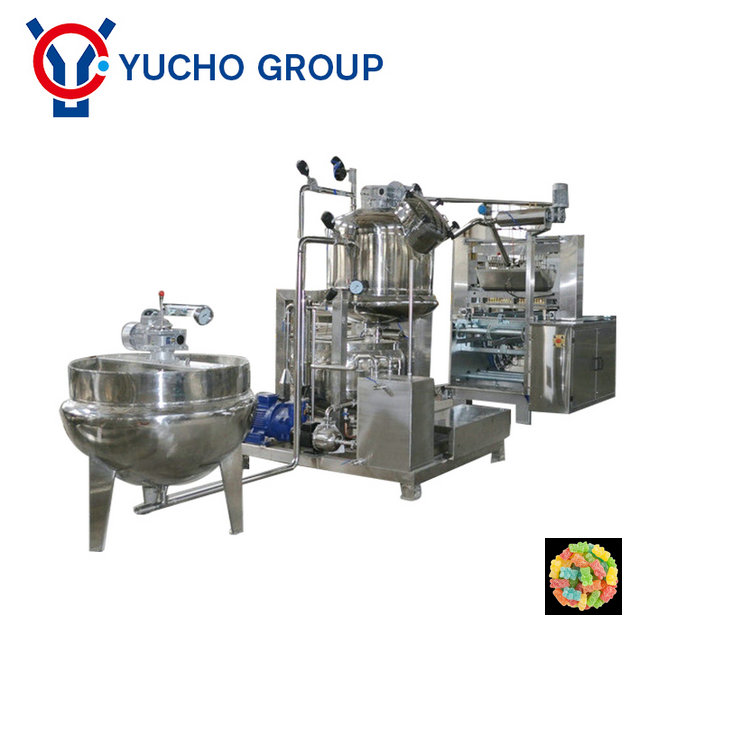
4. Coating and polishing machine
Once the fudge is shaped and cooled, it can be further processed to enhance its appearance and taste. To do this, use a coating and polishing machine to apply a thin layer of sugar or wax to the surface of the fondant. This gives the candies a smooth, shiny appearance with a hint of sweetness that enhances their flavor.
Coating and polishing machines are equipped with rotating drums or belts that gently roll the fondant as the coating is applied. This process ensures that the candy is evenly coated and polished, resulting in an even and attractive finish. Coating and polishing machines are particularly popular for gummy candies because they give the candies a unique shine and texture that is attractive to consumers.
5. Packaging equipment
The final step in gummy production is packaging. Packaging equipment is used to seal gummies into individual wrappers, bags or containers ready for distribution and consumption. This equipment may include automatic bagging machines, flow wrappers and labeling machines to streamline the packaging process and ensure the gummies are securely sealed and labeled.
Packaging equipment is designed to handle gummies of different shapes and sizes as well as a variety of packaging materials. It also has the ability to apply tamper-evident seals and date codes, ensuring the quality and safety of the gummies. Packaging equipment plays a vital role in the final presentation of the gummies, allowing them to reach retail shelves and be enjoyed by consumers.
The following are the technical parameters of gummy making equipment:
Technical Specifications
Model | GDQ150 | GDQ300 | GDQ450 | GDQ600 |
Capacity | 150kg/hr | 300kg/hr | 450kg/hr | 600kg/hr |
Candy Weight | as per the candy size | |||
Depositing Speed | 45 ~55n/min | 45 ~55n/min | 45 ~55n/min | 45 ~55n/min |
Working Condition |
Temperature:20~25℃;Humidity:55% |
|||
Total power | 35Kw/380V | 40Kw/380V | 45Kw/380V | 50Kw/380V |
Total Length | 18m | 18m | 18m | 18m |
Gross Weight | 3000kg | 4500kg | 5000kg | 6000kg |
Post time: Jan-31-2024